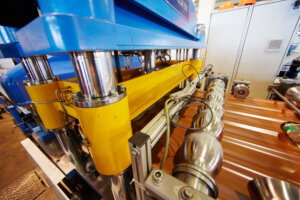
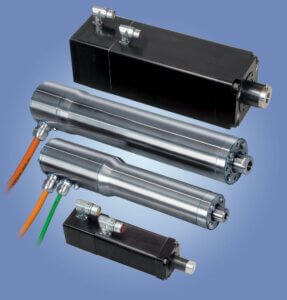
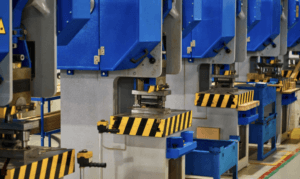
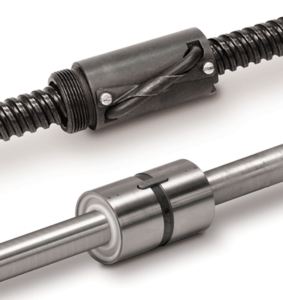
Actuator know-how for machine design engineers, Part 2
Machine designers face a variety of options when selecting linear actuators. It all comes down the best fit for the application: what solution provides the best results at a cost– effective price.
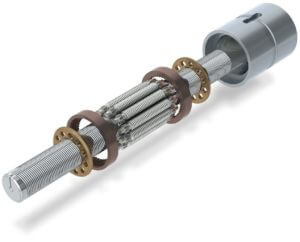
Roller screw technology for electric actuators
The unique design of a roller screw actuator offers longer life and higher thrust in a smaller package compared to ball screw actuators, increasing a machine designer’s ability to create compact machine concepts.
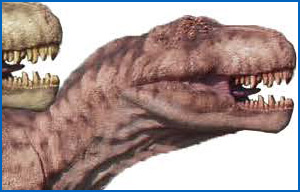
The Big Era of electromechanical linear actuators
Traditionally, hydraulic power is the go-to answer for heavy lifting. Now, high-force electric actuators have overtaken hydraulics in terms of flexibility, precision and reliability.
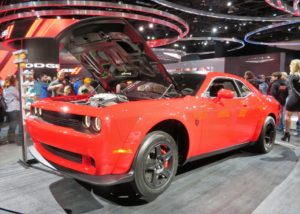
High-force linear actuator makes muscle car simulation possible
Tolomatic linear actuators are used worldwide in a myriad of industries for automation tasks like conveying, sorting, filling and more. Beyond conventional industrial applications they are also used in demanding, non-industrial applications. Some of these, such as simulators for flight, driving, testing and entertainment, require high-frequency moves to create a realistic experience. Here’s one such story, in which our electric high-force linear actuators helped simulate the experience of popping a wheelie in a true muscle car.
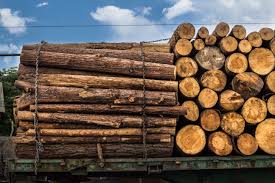
Extreme force electric linear actuator controls lumber drying
The lumber processing industry demands rugged, strong, reliable and accurate equipment in all its operations. Machine designers who serve this industry need extreme force linear actuators to move heavy loads. Hydraulic cylinders have been the go-to, but they have limitations, such as poor control, leaks, temperature sensitivity, maintenance requirements and lack of feedback. Now there are electric rod actuators powered by roller screws that can meet the requirements of these high force applications.
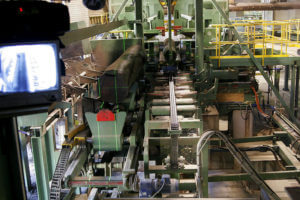
Roller screws for high force linear actuators. What type’s best?
Selecting the best screw type for a high force linear actuator can seem a daunting task, but it doesn’t have to be. Start with our Guide on the three common screw types for electric actuators, their advantages and disadvantages.
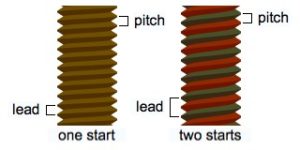
Acme, ball and roller screws for electric linear actuators
When you’re specifying a screw-driven electric linear actuator, you’ll need to consider the type of screw that best meets the needs of your specific application. Some manufacturers give you a choice so you can tailor the device precisely, and that’s a good thing since applications differ widely.
The basic types you’ll have to choose from are roller screws, ball screws and acme screws. There’s quite a lot a machine designer needs to know about these electric actuator screw types and how to select the right one. We offer a guide that helps your decision-making.
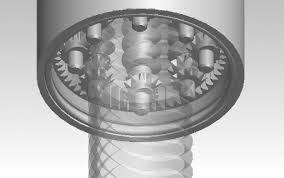
Electric high force linear actuators with roller screws rival hydraulic
When you’re specifying a high force linear actuator, your application’s requirements call the shots. It used to be that hydraulic cylinders were your only recourse when high force was needed. Now there are electric linear actuators with roller screws that rival the high force, high thrust, high torque capabilities of hydraulics. Plus, these electric actuators deliver high speed, great accuracy and repeatability and long life. Electric roller screw actuators are definitely an alternative to consider.
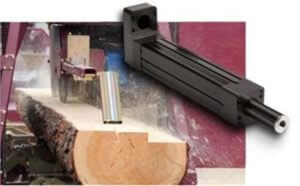
High force linear actuator: electric replaces hydraulic
It used to be that when a machine designer was confronted with a high force linear actuator application, the only solution was a hydraulic cylinder. That meant the designer had to factor in the bulky hydraulic power unit (HPU), the inevitable leaks of hydraulic fluid and the downtime produced by frequent maintenance.
Now there’s another option when a high force linear actuator is needed. There are electric linear actuator products that can meet demanding specifications with ease.