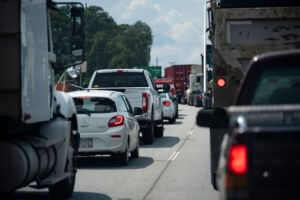
Achieve better quality welds with electric servo actuators
Car buyers demand top quality and durability in their vehicles. Automobile manufacturers strive to meet and even exceed these demands. The welds that hold a car’s body together are fundamental to the vehicle’s quality, so it’s essential that weld quality is the best.
Robots are often used in auto body welding because they’re fast and consistent. When it comes to controlling the weld gun, an automobile manufacturer has a choice: use a pneumatic actuator or an electric integrated servo linear actuator. An electric servo actuator will provide better weld quality, consistently.
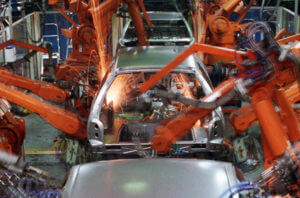
Electric servo actuators and welding robots build better autos faster
Robots are well-suited to high-volume processes like welding auto bodies because they can work quickly and consistently. Using electric servo actuators makes faster speeds and consistent weld quality possible while reducing costs.
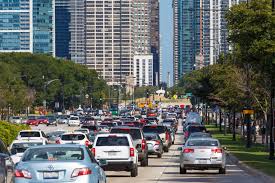
Lightweight servo actuators lower robotic RSW costs
Buyers want sturdy, well-built cars, so the quality of welds that hold auto bodies together is crucial to vehicle manufacturers. Manufacturers want strong welds that are consistently and accurately placed so the finished car looks both durable and attractive.
Welding robots for resistance spot welding (RSW) have been a boon to auto manufacturers because they provide consistent weld placement. But all welding robots need actuators to carry and power the weld gun. Those actuators have a huge impact on the consistent quality of welds. They can also impact the cost of robotic resistance spot welding.
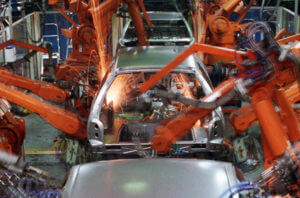
Servo welding actuators improve weld quality, reduce costs
Reducing manufacturing costs and improving product quality are driving forces in automotive manufacturing. Automation plays a key role in achieving these goals, and robots, especially welding robots, are an important part of the automation picture.
Resistance spot welding is used extensively in auto frame and body construction, and robotic welding lines are familiar sights in many plants. This type of welding requires speed, exact placement of welds, and precise pressure on weld tips. Most resistance spot welding robots rely on servo welding actuators to control cycle timing and pressure on weld tips.

Better welds with electric linear actuators for resistance welding robots
U.S. and European car manufacturers have long been convinced of the benefits of automation in their production facilities. Spot welding robots are common in their body production lines.
Automation and robotics offer advantages in cost savings and quality, but plants in India, China, and Southeast Asia have been slow to get on the bandwagon. Perhaps some plant managers see these production processes as too expensive or difficult to implement. Whatever the reason, that situation may be changing according to a Frost & Sullivan study described in an article on The Fabricator.com