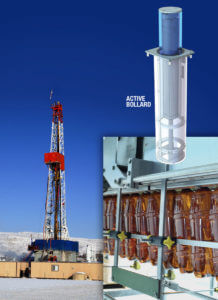
Avoid the pitfalls, gain all the benefits of replacing hydraulics with electric actuators
Electric actuators continue to find new and exciting places within automation processes from the mundane to some of the most extreme operating environments on the planet. Everyday machine designers seek alternative electric solutions to hydraulic cylinders for the very first time. However, there are many common pitfalls to properly sizing an electric equivalent. When sized correctly, replacement with high-force electric linear actuators can provide tremendous benefit in processes, quality and reducing your total cost of ownership.
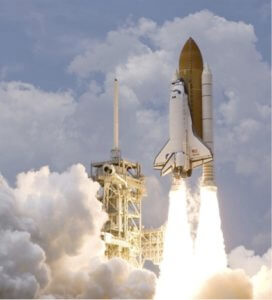
Failure not an option? How to avoid premature linear screw actuator failure
Some components are more mission-critical than others. A main worry of machine design engineers is making equipment that will last and avoiding need for field service calls to diagnose issues and replace failing components. At their core, electric linear screw actuators deploy mechanical technology such as ball bearings, ball screws and roller screws that have a finite life. These components do not last forever, even though that is the expectation of some customers. When asked “How long will this actuator last?” we provide our customers with a way to calculate, estimate and size the electric linear screw actuator to achieve the desired life for their applications.
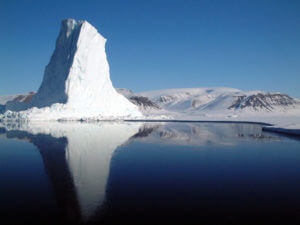
Need low cost linear motion? Total cost of ownership is key
How are industrial linear motion components like icebergs?
They say 90% of an iceberg’s volume is hidden under water. When you buy linear motion components, specifically hydraulic and pneumatic cylinders, the real cost may be hidden as well. If you’re looking for low cost linear motion, you may be attracted to the low purchase price of fluid power cylinders. However, purchase price is just the tip of the iceberg. To get a true picture, you need to look at total cost of ownership (TCO), including the long-term operating costs of the equipment.
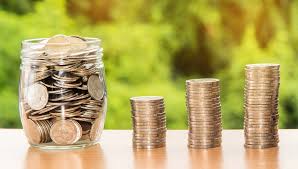
How to ensure low cost linear motion
“People want to save money on their industrial automation systems,” says captain obvious. Equally obvious is the fact that no one wants to reduce output or product quality to save a buck. So how does a machine designer accomplish this? Save money without sacrificing performance and quality?
One way to ensure affordable automation systems and, specifically, low cost linear motion, is to stop looking at purchase price only and start thinking long term. Consider the total cost of ownership (TCO) of the equipment.
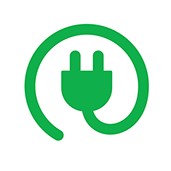
The great debate: Electric linear actuators vs. pneumatic
There’s a new debate in motion among machine designers. What’s best? Pneumatic or electric linear actuators? The truth is it depends on the application. What follows is an honest comparison of linear actuator choices – an assessment of strengths and weaknesses – so you can choose what’s best for your project.
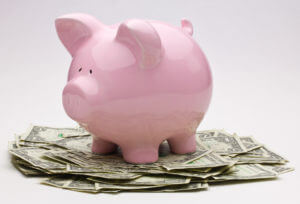
Total cost of ownership: pneumatic vs electric linear actuators
Who doesn’t like to save money? We’re all in search of a good deal, but how do you define what’s good? If you buy something on the cheap but it falls apart in a short time, is that a good deal? Maybe it’s smarter to pay more for something that last longer and performs better.
In business, this means considering total cost of ownership (TCO), that is, initial acquisition cost plus operating costs. Comparing TCO to purchase price alone is especially interesting when applied to pneumatic and electric linear actuators.
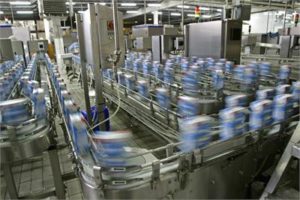
Electric linear actuator speeds up changeovers, lowers TCO
Time is money, as the saying goes, and it’s especially true in manufacturing. Reduce the time a process takes and you save operating costs. The concept of total cost of ownership (TCO) considers issues beyond a component’s purchase price like the downtime and labor costs associated with changing production set-ups.
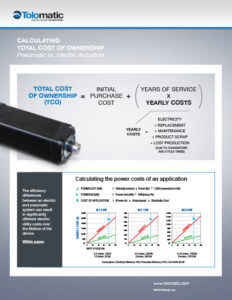
Calculating total cost of linear actuators [INFOGRAPHIC]
Not too long ago many machine designers only considered the purchase price of automation components, like linear actuators, when they analyzed cost. And manufacturing management only looked at acquisition cost when they considered investing in automation.
Now machine designers and manufacturers are using a more thorough approach to cost analysis. Rather than looking at purchase price alone, they are looking into the “total cost of ownership” of a component, machine or technology. It's a business finance concept, used frequently when considering computer system upgrades.
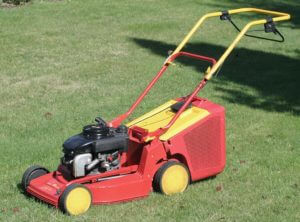
Integrated linear actuator increases manufacturing efficiency
Production cost and efficiency are important considerations in all manufacturing, but these factors take on critical status in some segments. Small-engine production is one of these. Using the right linear actuator can boost efficiency and reduce cost.
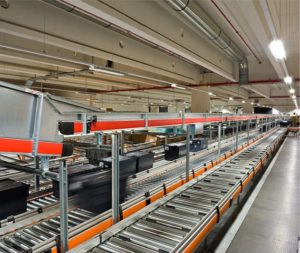
Electric cylinders lower cost of conveying equipment
Conveying equipment manufacturers know that fast and efficient systems are critical to manufacturing success. Conveying system buyers are demanding better positioning accuracy, energy efficiency, and lower cost of ownership to ensure their ongoing success. Plus, some are eliminating compressed air systems and asking for electric linear actuators, including electric cylinders, instead of pneumatic solutions. Since they often produce several product models in the same plant, buyers need actuators that are easily programmable to several positioning set-ups.
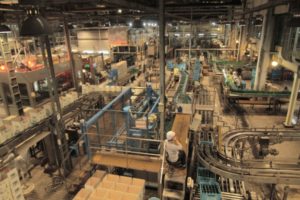
Electric linear actuators versus pneumatic: Total cost of ownership
Saving money is on everyone’s mind these days, especially when it comes to industrial automation. Automation is recognized as an important way to boost quality and productivity; however, the cost of adding automated systems can be daunting.
To keep costs in line, machine designers are often tasked with finding money-saving solutions. This doesn’t mean using the cheapest components, though. If a component has a low purchase price but is expensive to operate and maintain, it’s not a bargain. Smart engineers look at the total cost of ownership (TCO) of components they’re considering, including linear actuators.