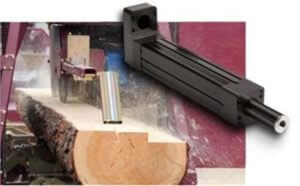
High force linear actuator: electric replaces hydraulic
It used to be that when a machine designer was confronted with a high force linear actuator application, the only solution was a hydraulic cylinder. That meant the designer had to factor in the bulky hydraulic power unit (HPU), the inevitable leaks of hydraulic fluid and the downtime produced by frequent maintenance.
Now there’s another option when a high force linear actuator is needed. There are electric linear actuator products that can meet demanding specifications with ease.
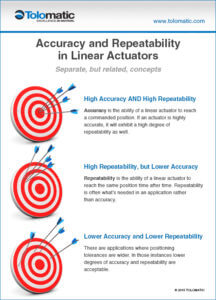
Electric linear actuator accuracy and repeatability webinar
When an engineer is developing a machine design, accuracy is often top-of-mind. So is machine cost. But these two considerations can be at odds since the usual scenario is that the higher the accuracy of a device, the higher the cost. This certainly holds true for electric linear actuators and linear motion systems.
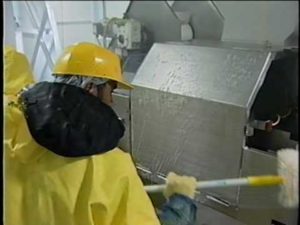
Electric linear actuators meet the challenge of FSMA
The federal Food Safety Modernization Act (FSMA) that was enacted in 2011 has energized the food industry around food safety and the prevention of food-borne illnesses. Most of the major producers and food equipment manufacturers have kept ahead of FSMA requirements successfully since food safety and prevention have always been among their top priorities.
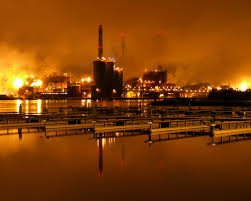
High force linear actuators: hydraulic vs roller screw actuators
Hydraulic cylinders have long been a leading choice for factory automation equipment needing a high force linear actuator. However, there have been advances in electric actuation (for example, the availability of roller screw actuators) which make these electric actuators suitable now for many high force applications.
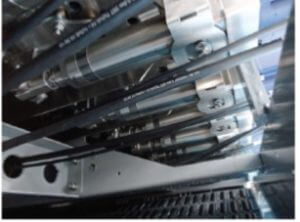
Electric actuator life in units of time: ball & roller screw actuators
A machine’s useful life depends on the life of its critical components. And machine designers frequently hear the question, “How long can I expect this machine to keep working?”
When electric linear actuators are used, calculating life can be straight-forward for ball screw and roller screw actuators. Since these screw types incorporate rolling elements as essential parts, you can use the L10 life formula for ball bearings.
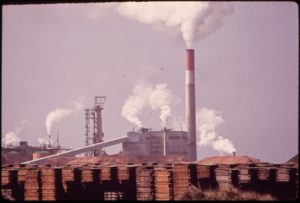
Solid-bearing, belt-driven linear actuator handles harsh environment
Many applications call for the carrying action of a rodless electromechanical actuator. And many of these need the high speed and long stroke capabilities of a belt-driven linear actuator. But what do you do when your application is in a dusty, harsh environment? Many rodless electromechanical actuators can’t handle these conditions. Their roller bearings get clogged with dust and stop working. Could a solid bearing be the solution?
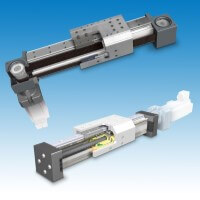
Selecting a rodless electromechanical actuator: belt- vs. screw-driven
Let’s say you’ve decided you need a rodless electromechanical actuator to carry a load in your application. Now you have to select a linear drive system. The two most common choices are screw drives and belt drives. Both drive types offer long life, low maintenance, and efficiency in converting the motor’s rotary motion to the carrier’s linear motion. However, each drive type is more suited to particular applications than others, depending on a few key factors.
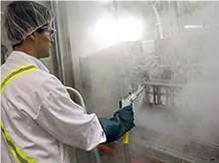
Electric linear actuator is clean-in-place, washdown ready
Stringent regulations govern the food processing industry. Food processing equipment and components, like electric linear actuators, must meet food safety regulations and stand up to clean-in-place (CIP) procedures. Food industry cleaning procedures may include regular washdowns with hot water, steam, high pressures, and caustic chemicals. Corrosion resistant materials and a water-shedding design are musts.
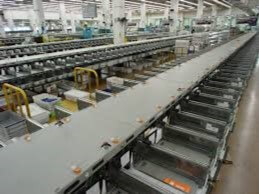
Linear actuator helps convert conveyor to electric
Every factory relies on some kind of conveyor system to take components, work pieces, or finished goods from one place to another. In fact, most factories have several conveying systems, each tailored to a specific need. Conveying equipment is varied and essential. Components in these systems, like linear actuators, must be able to meet these varied needs and provide reliable performance.
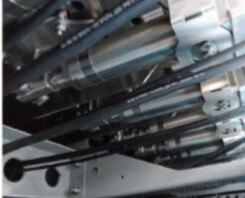
“How long will this actuator last?”
“How long will it last?” Every machine design engineer gets asked this question and will have to calculate the anticipated life of the machine – life that’s based on machine components including linear actuators. Engineers also have to consider expected life when they’re evaluating competing components.