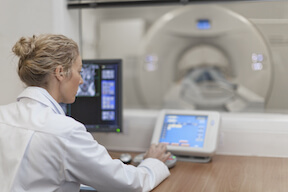
Motion control solutions for medical device applications
Solutions for medical procedures include equipment for radiation treatment, a contrast dye injection, and a specialty machine that safely performs scans on large animals.
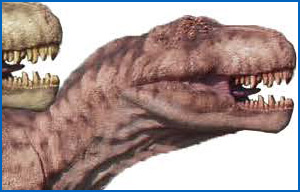
The Big Era of electromechanical linear actuators
Traditionally, hydraulic power is the go-to answer for heavy lifting. Now, high-force electric actuators have overtaken hydraulics in terms of flexibility, precision and reliability.
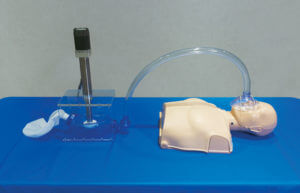
Automating the squeeze: Tolomatic prototype improves on hand-held emergency ventilator for COVID-19 patients
Our prototypes use electric linear actuators to automate a hand-held, portable and non-invasive emergency ventilator. The advantage of screw-driven linear actuators is that they provide smooth and consistent operation--allowing the device to control the velocity, the acceleration and the distance of any move at any point in time. This controlled motion allows for a more continuous volume of air per compression cycle and a more typical breathing cycle.
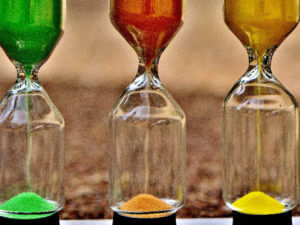
How to Calculate Electric Linear Actuator Lifespan
Every machine design engineer gets asked about the anticipated life of their machine—life that’s based on machine components including electric linear actuators. Also, expected service life is a factor engineers consider when they’re evaluating competing components.
Calculating electric linear actuator life can be straight-forward for ball screw and roller screw actuators. You use the L10 life formula for ball bearings. Here's a summary of the method.
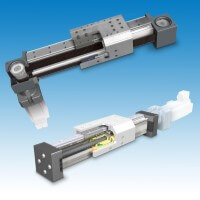
Timing belt or power screw drive: What’s best for a rodless actuator?
As a designer, you may be faced with an application in which you have to carry and support a load as well as move it. These are ideal applications for rodless electromechanical actuators.
While determining which rodless actuator model will suit your needs, you'll also need to select the type of drive: belt or screw. This blog will briefly explain these drive systems and summarize their advantages and disadvantages
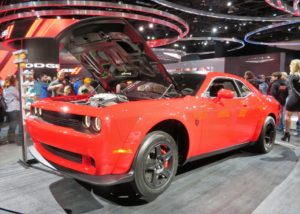
High-force linear actuator makes muscle car simulation possible
Tolomatic linear actuators are used worldwide in a myriad of industries for automation tasks like conveying, sorting, filling and more. Beyond conventional industrial applications they are also used in demanding, non-industrial applications. Some of these, such as simulators for flight, driving, testing and entertainment, require high-frequency moves to create a realistic experience. Here’s one such story, in which our electric high-force linear actuators helped simulate the experience of popping a wheelie in a true muscle car.
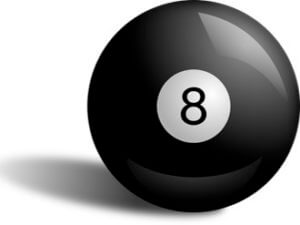
Electric linear motion vs. pneumatic. 8 things every designer should know about selection
There’s a debate in the machine design community about what’s the best linear motion technology—electric or pneumatic. There are proponents on both sides. As a manufacturer of both electric and pneumatic linear actuators, we’d like to bring some balance to the discussion.
Electric linear motion has benefits as do pneumatic solutions. This blog will give you eight factors to consider when you’re making this important selection
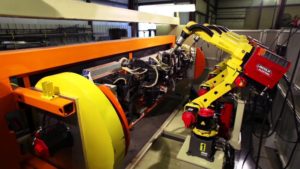
High-force linear actuators. Roller screws vs. ball screws
Not too long ago the only solution for high-thrust linear motion was fluid-powered cylinders that used high-pressure air or hydraulic oil. Although these cylinders could provide the force required, they could not deliver on requirements for infinite positioning, speed control, and low maintenance.
Now there are electric rod actuators that deliver high forces and excel at the other criteria as well. Often these electric high-force linear actuators utilize ball or roller screws. However, it’s a challenge to choose the right screw technology for a high-force application.

What’s best? Integrated linear actuators or traditional.
When you’re faced with designing a new piece of automation equipment, you have a lot on your mind. Concerns like performance requirements. How to design flexibility into the machine. How to keep costs down. How to pack the performance needed into a compact package.
You can rely to electric linear actuators to address these issues. They have inherent flexibility and long-term cost-efficiency. Once you choose electric linear motion, you can select either an integrated linear actuator or a traditional design. Both options have pluses and minuses that we’ll review here.
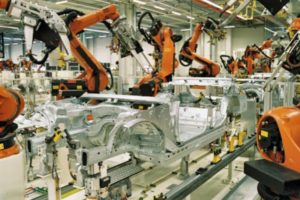
Innovate with linear motion: Online resource for integrating electric actuators into machine designs
For every application a machine designer tackles, they have to consider a unique set of requirements. Evaluating a variety of linear motion attributes is key to determining the optimal solution.