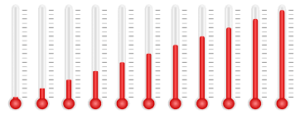
Chilly or scorching: linear servo actuator works in all temps
Machine designers know the problems hydraulic cylinders have in cold and hot weather – sluggish response due to thicker oil on the one hand and extensive maintenance downtime on the other caused by frequent seal failure. Plus, there’s the always-present threat of a costly fluid leak. An electric linear servo actuator can solve these challenges and lower operating costs at the same time.
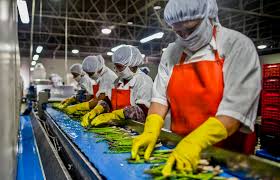
What to consider: electric actuators for food and beverage processing
Keeping things clean is a top concern in food and beverage processing operations because food safety is crucial. The Food Safety Modernization Act (FSMA), with its emphasis on preventing foodborne illness, puts even more pressure on food producers. Machine designers who serve this industry need to incorporate components that meet the industry’s demands. When it comes to electric linear actuators, there are several things a design engineer needs to consider, especially if the machine will be subjected to periodic washdowns.
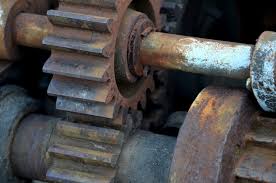
Stainless steel linear actuators stand up to corrosion, tough conditions
Machine designers who develop systems for harsh environments often need corrosion resistant components, including stainless steel linear actuators, to stand up to challenging environmental conditions. Corrosive agents, moisture and dust in manufacturing environments impact the performance and life of automationn components. Dust and debris may enter housings causing wear. Moisture may short electrical connections. Corrosive agents can eat away at housings, seals, fasteners and more. For confirmation that a component will stand up to environmental factors, we recommend the IP (International Protection or Ingress Protection) rating system.
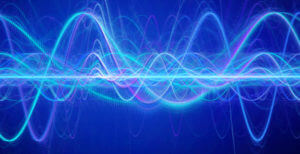
Hush! Minimizing noise in electric linear motion systems
Under most circumstances electric linear motion systems are quiet. They certainly don’t create the hissing and bang-bang noises associated with pneumatic systems. However, there’s another type of noise that comes with electric systems of all types – electrical noise or interference.
This is a common occurrence caused by random fluctuations in electrical signals. If the amplitude gets high enough, electrical noise can disrupt the operation of devices like electric linear actuators. The results can be anything from erratic movements to complete system failure.
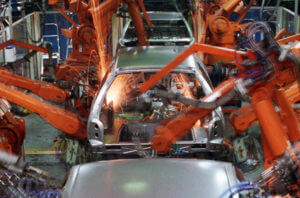
Electric servo actuators and welding robots build better autos faster
Robots are well-suited to high-volume processes like welding auto bodies because they can work quickly and consistently. Using electric servo actuators makes faster speeds and consistent weld quality possible while reducing costs.
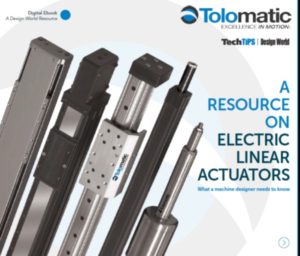
Electric linear motion. Selecting linear actuators.
Linear actuators are familiar components in many factory automation systems. They’re one of the usual suspects in any line-up of linear motion components.
There’s a lot riding on specifying the right linear actuator for the task. Choose well and it’s smooth sailing. The actuator performs without a glitch for a long time. Choose the wrong one, and it’s a bumpy ride. You can wind up with break-downs and poor product quality.
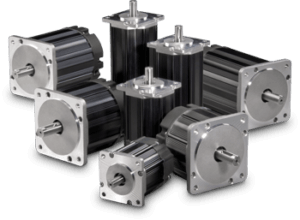
Motor selection for electric linear motion. Stepper vs servo
An electric linear motion system needs a motor. Unlike pneumatic cylinders that are powered by a central air compressor, electric linear actuators are powered by electric motors. The mechanisms in the actuator convert the motor’s rotary motion into linear motion. Machine designers can choose either servo or stepper motors for their electric linear actuator applications.

Selecting a choke valve operator for MPD. What’s best?
As oil and gas drilling environments grow more challenging, the need for the enhanced control provided by managed pressure drilling (MPD) grows too. The drilling choke valve is an essential component in an MPD system, and the drilling choke valve operator (choke valve actuator) provides the vital element of control. It’s the valve operator that communicates the control software’s commands and provides position feedback to the control system. It stands to reason that selecting the best valve operator is critical to the success of an MPD system.
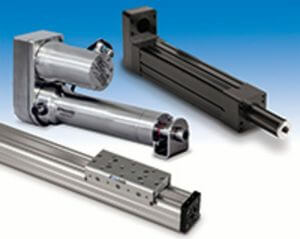
Selection tips: rodless electromechanical & electric rod actuators
When you specify a linear actuator, some basic decisions come first. Like electric or fluid-powered?Like do you need the push/pull of an electric rod actuator or the load-carrying action of a rodless electromechanical actuator?
We’ve compiled tips for selecting these actuator types. Here’s an opportunity to increase your knowledge of electric linear motion.
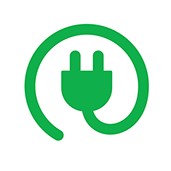
The great debate: Electric linear actuators vs. pneumatic
There’s a new debate in motion among machine designers. What’s best? Pneumatic or electric linear actuators? The truth is it depends on the application. What follows is an honest comparison of linear actuator choices – an assessment of strengths and weaknesses – so you can choose what’s best for your project.