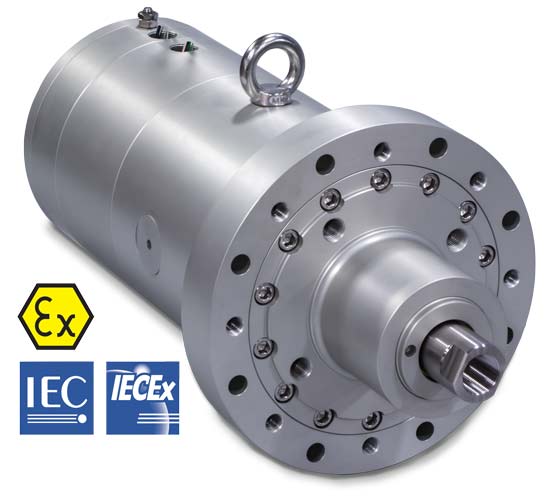
ServoChoke® SVC Electric Choke Valve Actuator / Operator
ServoChoke® SVC is a high performance linear integrated electric choke valve actuator that meets the rigorous needs of the oil and gas industry. The SVC provides a more reliable, high-speed, precision electric choke operator in performance drilling applications vs. conventional hydraulics or jack screw assemblies. The ServoChoke SVC is perfect for Managed Pressure Drilling (MPD), Set-point choke control and Choke & Kill for well control applications.
ServoChoke electric choke valve actuators include an integrated servo motor, gear box and planetary roller screw to enable quick and continuous modulation with highest accuracy. With global certifications for ATEX, IECEx, and Class I Div. 1 together with a temperature rating of -40° C to +60° C, the all steel SVC choke actuator is designed to perform in the harshest environments.
- Globally certified: CID1 • ATEX • IECEx
- Worry-free performance in the most hazardous location environments
- Speeds up to 19.6 mm/sec (0.77″/sec) – open/close choke in less than 3.2 seconds
- 3 mm (0.125″) adjustments happen in less than 0.5 second
- Temperature range: -40° to +60°C (-40° to +140° F)
- Positional repeatability to within 0.08% of span or better
- Planetary roller screw for long life and no maintenance
- Fully integrated motor/actuator/feedback in a single, sealed housing
- Rugged NACE MR0175 compliant steel body
Contact Tolomatic to learn more about how our high performance electric choke valve actuators can meet the particular needs of your unique drilling application.
View the video interview at the IADC Managed Pressure Drilling & Underbalance Conference
Features & Ordering
ServoChoke Electric Choke Valve Actuator
ServoChoke is a high performance linear integrated actuator designed to meet the rigorous needs of the oil and gas industry. With global certifications, an all-steel NACE MR0175 compliant body and a temperature range of -40°C to +60°C, ServoChoke is capable of providing reliable, fast, and precise positioning. The brushless servo motor, absolute encoder, and roller screw drivetrain ensure the durability and reliability needed for a wide variety of environments.
Review this graphic for a closer look at some of the unique design aspects that make the SVC the ideal actuator for choke valve applications.
What is ServoChoke?
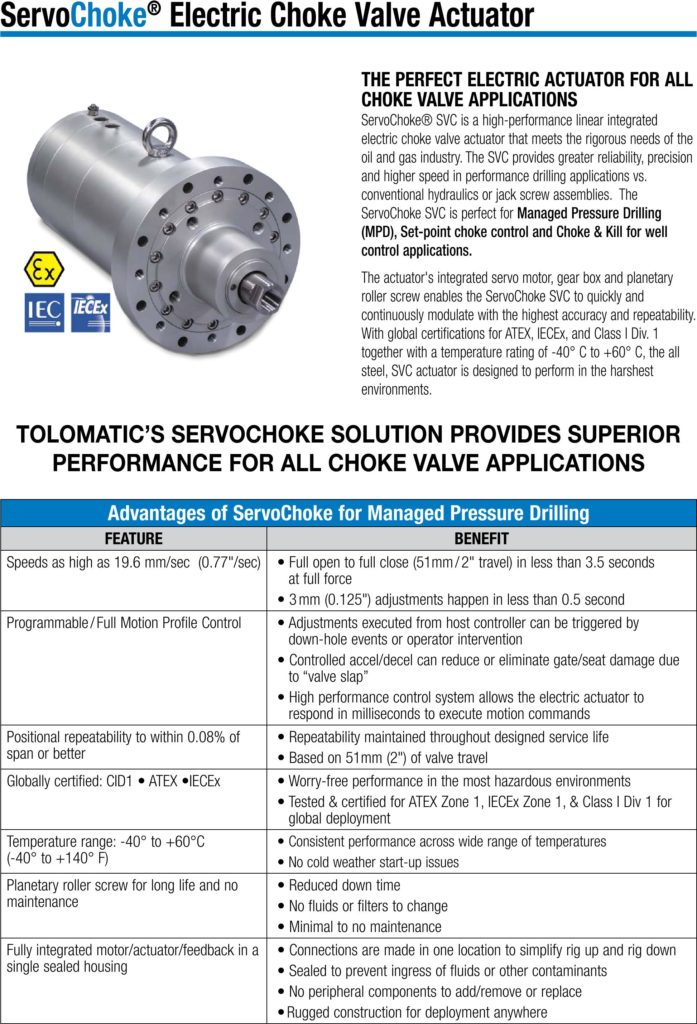
ServoChoke Features
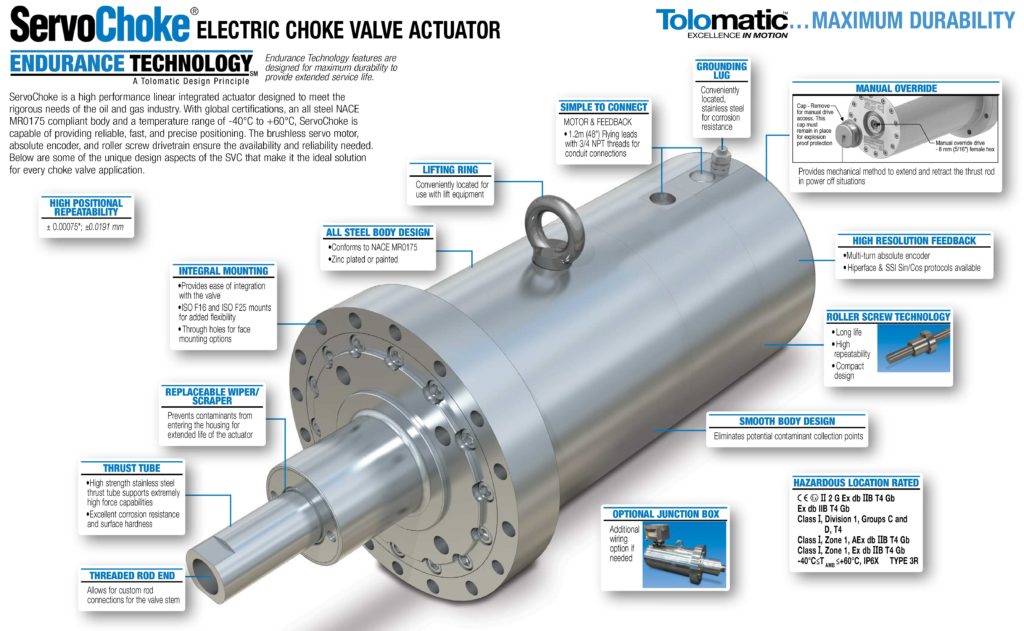
ServoChoke Actuator & Drive System
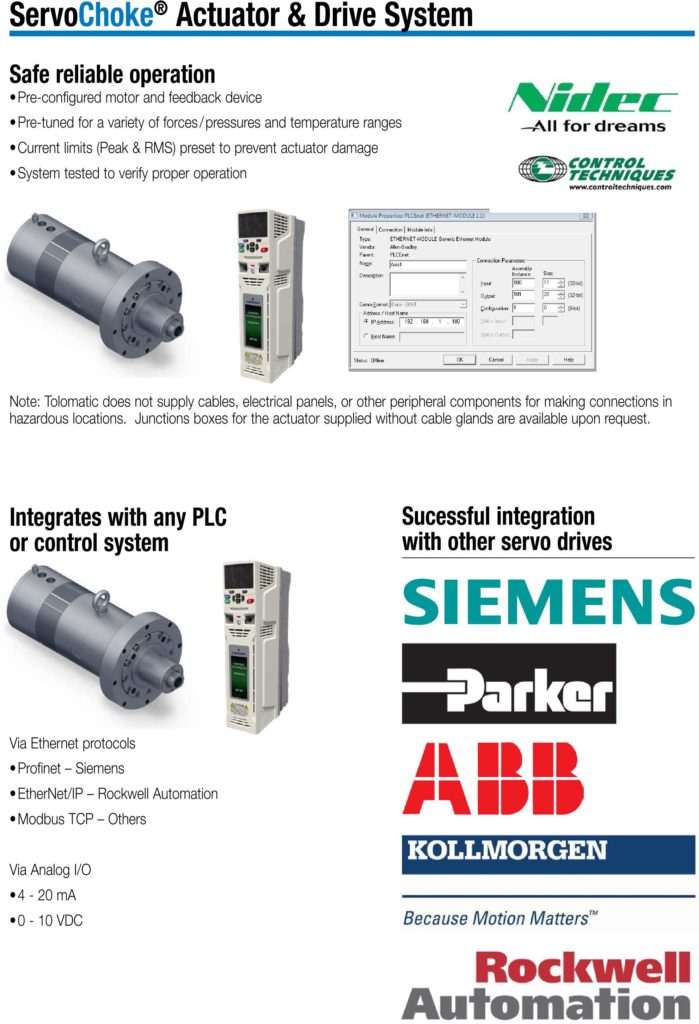
Testing and Simulation
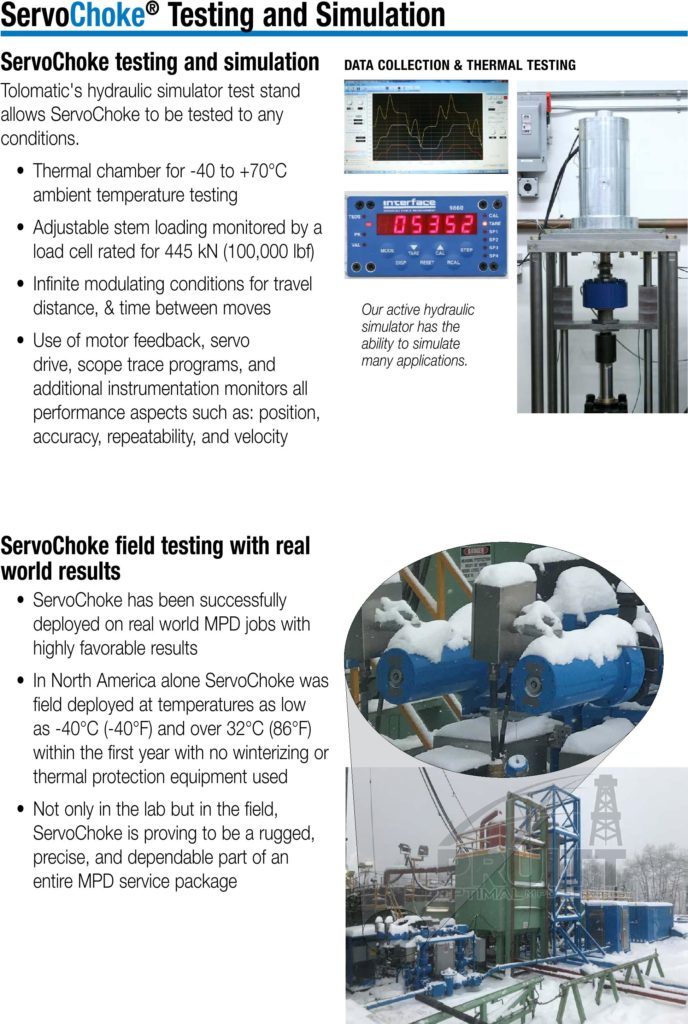
Superior to Hydraulic & Hybrid Systems
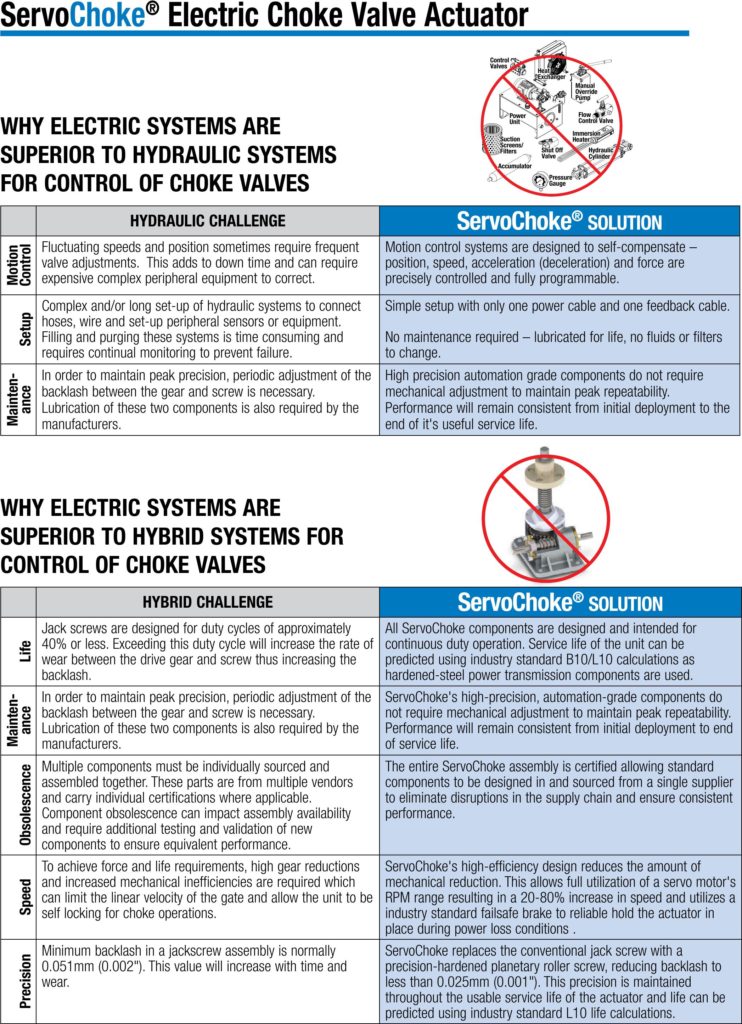
Flow Loop Tested at PERTT Labs LSU
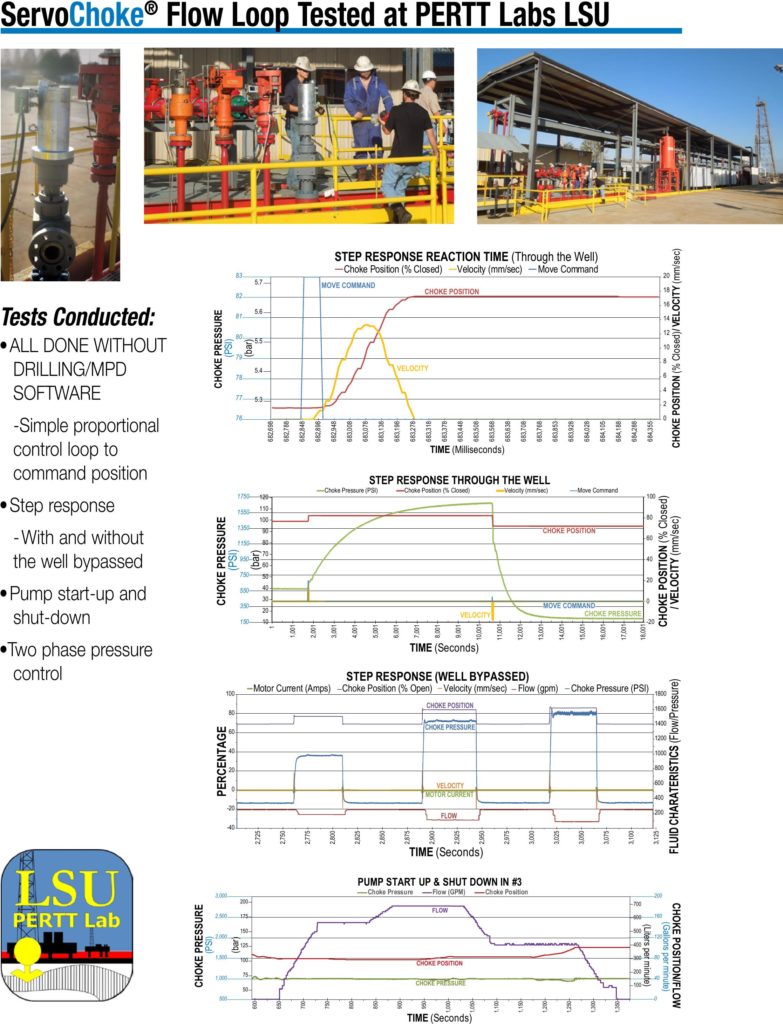
ServoChoke Features & Options
ServoChoke Electric Choke Valve Actuator and Drive System
Safe, reliable operation of both the electric valve choke actuator and drive system.
- Pre-configured motor and feedback device
- Pre-tuned for a variety of forces/pressures and temperature ranges
- Current limits (Peak & RMS) preset to prevent actuator damage
- System tested to verify proper operation
- Integrates with any PLC or control system
- Successful integration with servo drives from Siemens, Parker, ABB, Kollmorgen, Rockwell Automation and Nidec
ServoChoke Testing and Simulation
Tolomatic’s hydraulic simulator test stand allows ServoChoke to be tested to any conditions.
- Thermal chamber for -40 to +70°C ambient temperature testing
- Adjustable stem loading monitored by a load cell rated for 445 kN (100,000 lbf)
- Infinite modulating conditions for travel distance, and time between moves
- Use of motor feedback, servo drive, scope trace programs, and additional instrumentation monitors all performance aspects such as position, accuracy, repeatability, and velocity
ServoChoke Field Testing With Real World Results
- ServoChoke has been successfully deployed on real-world MPD jobs with highly favorable results
- In North America alone ServoChoke was field deployed at temperatures as low as -40°C (-40°F) and over 32°C (86°F) within the first year with no winterizing or thermal protection equipment used
- Not only in the lab but in the field, ServoChoke is proving to be a rugged, precise, and dependable part of an entire MPD service package
Why Electric Actuators Are Superior to Hydraulic Systems for Control of Choke Valves
MOTION CONTROL
HYDRAULIC CHALLENGE
Fluctuating speeds and positions sometimes require frequent valve adjustments. This adds to down time and can require expensive complex peripheral equipment to correct.
ServoChoke SOLUTION
Motion control systems are designed to self-compensate — position, speed, acceleration (deceleration) and force are precisely controlled and fully programmable.
HYDRAULIC CHALLENGE
Complex and/or long set-up of hydraulic systems to connect hoses, wire and set-up peripheral sensors or equipment. Filling and purging these systems is time consuming and requires continual monitoring to prevent failure.
ServoChoke SOLUTION
Simple setup with only one power cable and one feedback cable. No maintenance required — lubricated for life, no fluids or filters to change.
HYDRAULIC CHALLENGE
In order to maintain peak precision, periodic adjustment of the backlash between the gear and screw is necessary. Lubrication of these two components is also required by the manufacturers.
ServoChoke SOLUTION
High precision automation grade components do not require mechanical adjustment to maintain peak repeatability. Performance will remain consistent from initial deployment to the end of its useful service life.
Why Electric Systems Are Superior to Hybrid Systems for Control of Choke Valves
Life
HYDRAULIC CHALLENGE
Jack screws are designed for duty cycles of approximately 40% or less. Exceeding this duty cycle will increase the rate of wear between the drive gear and screw thus increasing the backlash.
ServoChoke SOLUTION
All ServoChoke components are designed and intended for continuous duty operation. Service life of the unit can be predicted using industry standard B10/L10 calculations as hardened-steel power transmission components are used.
Maintenance
HYDRAULIC CHALLENGE
In order to maintain peak precision, periodic adjustment of the backlash between the gear and screw is necessary. Lubrication of these two components is also required by the manufacturers.
ServoChoke SOLUTION
ServoChoke’s high-precision, automation-grade components do not require mechanical adjustment to maintain peak repeatability. Performance will remain consistent from initial deployment to end of service life.
Obsolescence
HYDRAULIC CHALLENGE
Multiple components must be individually sourced and assembled together. These parts are from multiple vendors and carry individual certifications where applicable. Component obsolescence can impact assembly availability and require additional testing and validation of new components to ensure equivalent performance.
ServoChoke SOLUTION
The entire ServoChoke assembly is certified allowing standard components to be designed in and sourced from a single supplier to eliminate disruptions in the supply chain and ensure consistent performance.
Speed
HYDRAULIC CHALLENGE
To achieve force and life requirements, high gear reductions and increased mechanical inefficiencies are required which can limit the linear velocity of the gate and allow the unit to be self locking for choke operations.
ServoChoke SOLUTION
ServoChoke’s high-efficiency design reduces the amount of mechanical reduction. This allows full utilization of a servo motor’s RPM range resulting in a 20-80% increase in speed and utilizes an industry standard failsafe brake to reliably hold the choke actuator in place during power loss conditions.
Precision
HYDRAULIC CHALLENGE
Minimum backlash in a jackscrew assembly is normally 0.051mm (0.002″). This value will increase with time and wear.
ServoChoke SOLUTION
ServoChoke replaces the conventional jack screw with a precision-hardened planetary roller screw, reducing backlash to less than 0.025mm (0.001″). This precision is maintained throughout the usable service life of the choke actuator and life can be predicted using industry standard L10 life calculations.
SVC Ordering
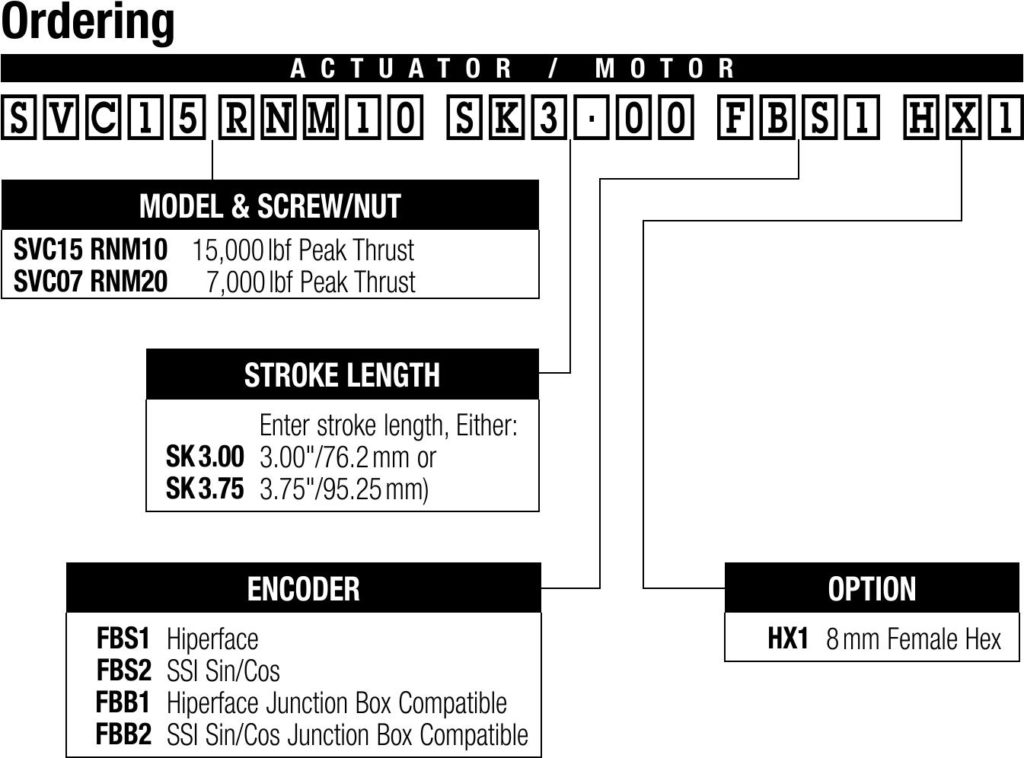
Specifications
Performance & Specifications
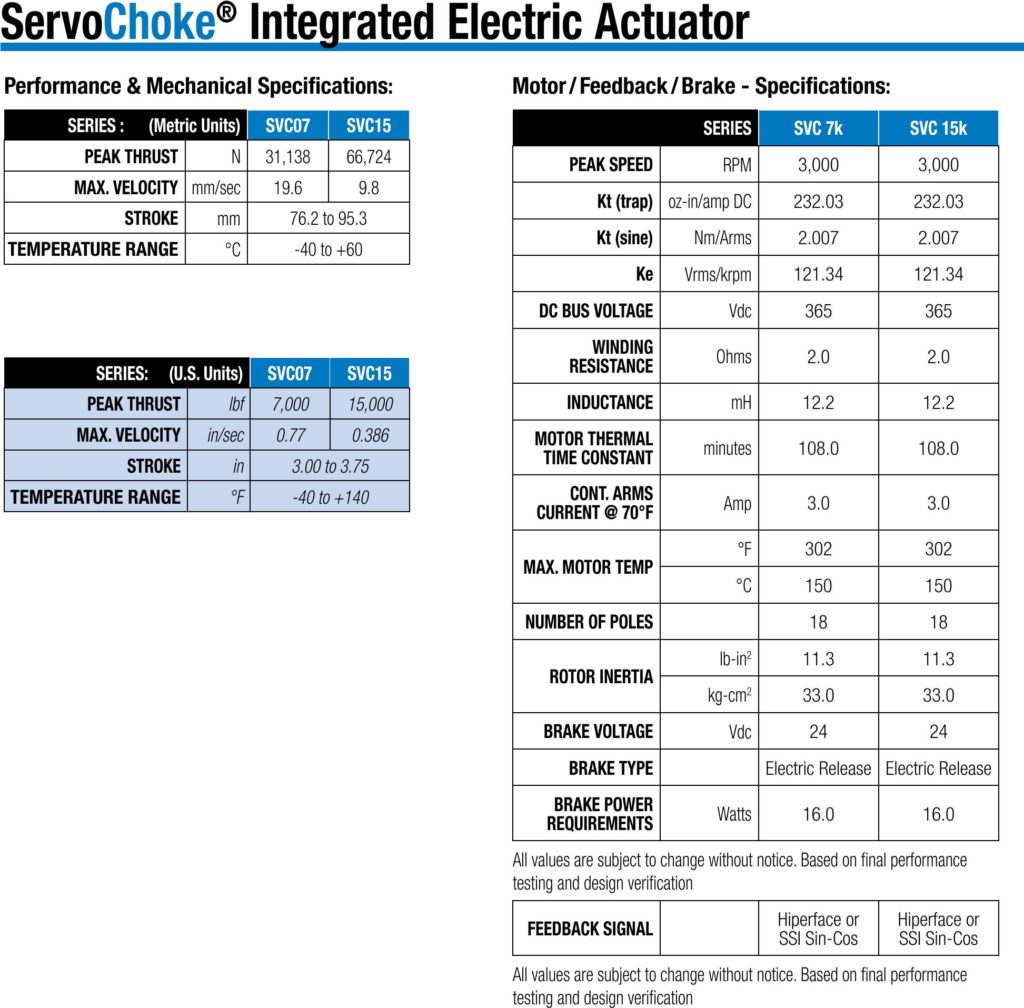
Dimensions
ServoChoke Dimensions
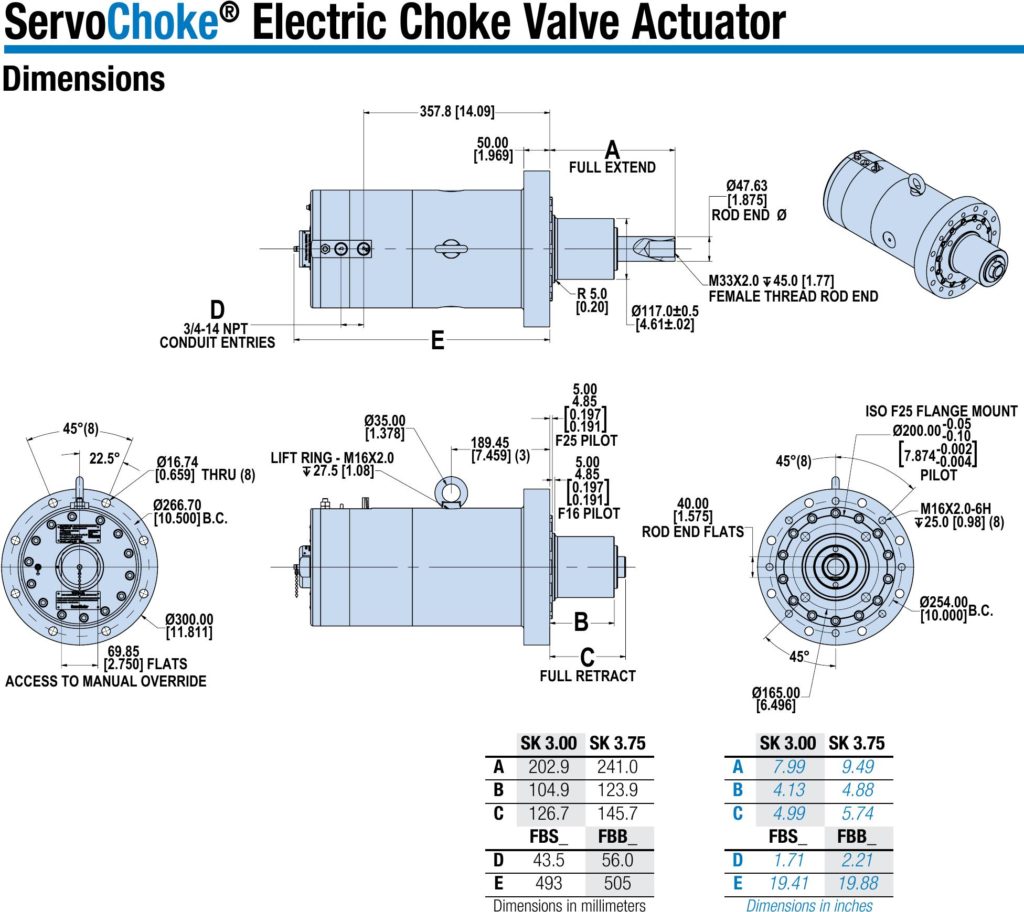
Additional Resources
Information Center:
Catalogs & Brochures
- Corporate Overview-Linear Motion Solutions Brochure (English)
- SOLUCIONES DE CONTROL DE MOVIMIENTO (Spanish, Corporate Overview-Motion Control Solutions Brochure)
- Unternehmensübersicht (German, Corporate Overview brochure)
- 公司概述 (Chinese, Corporate Overview Brochure)
- Brochure sur l'entreprise Tolomatic (French, Corporate Overview-Linear Motion Solutions Brochure)
- ServoChoke® Integrated Electric Actuator
- ServoChoke®集成电动推杆-中文 (ServoChoke® Integrated Electric Actuator-Chinese)
- OEM Actuator Solutions Brochure
Certifications
- ISO 9001 Certificate
- ServoChoke Certificate: Class I, Division 1, Groups C & D; Tcode: T4
- ServoChoke Certificate: INTERNATIONAL ELECTROTECHNICAL COMMISSION IEC Certification Scheme for Explosive Atmospheres
- ServoChoke Certificate: EU-Type Examination
- ServoChoke SVC 7K & SVC 15k EU Declaration of Conformity